History
From its formation in 1925 until the early 2000s, when the group turned its focus to real estate, the textile industry was its main business.
Its primary subsidiary, UTEXAFRICA, whose plants produced more than 30 million meters of fabric annually, was involved in every step of cotton processing. At its peak, the textile business employed up to 6,000 people in Kinshasa, making it the city’s biggest private employer at the time, and supervised more than 100,000 smallholders in the cotton sector, spread over several provinces in central and eastern Congo.
Over time, TEXAF has also diversified its business interests into metal construction, sandstone quarrying and digital investment.
These are some of the key dates in the history of the group:
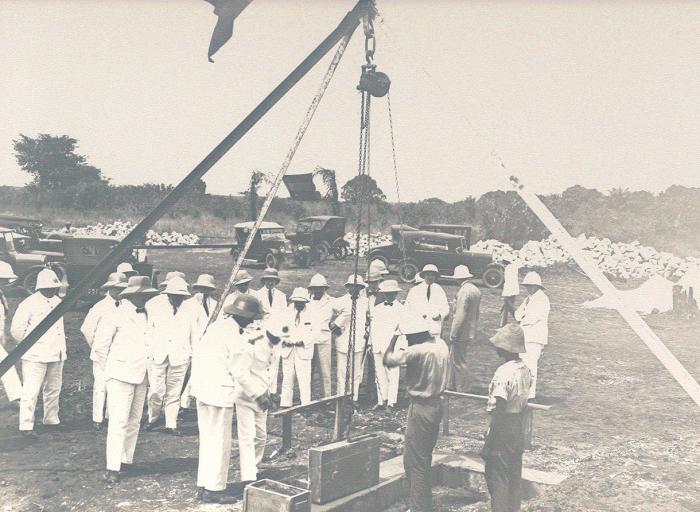
The textile factory was officially opened by King Albert I of Belgium at its present location in the bay of Ngaliema (Kinshasa), where milling, weaving and dying were carried out. To secure its energy and water supply, the group formed the Société des Forces Hydro-électriques de Sanga and the Société de Distribution d’Eau de Léopoldville.
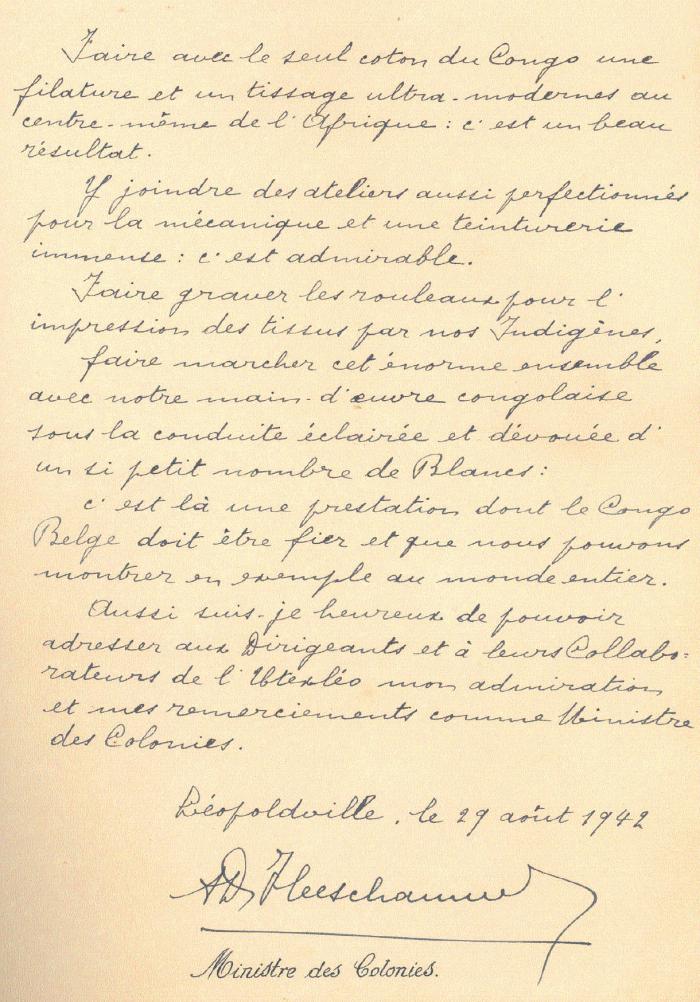
The company increased production considerably for the benefit of the allied war effort.
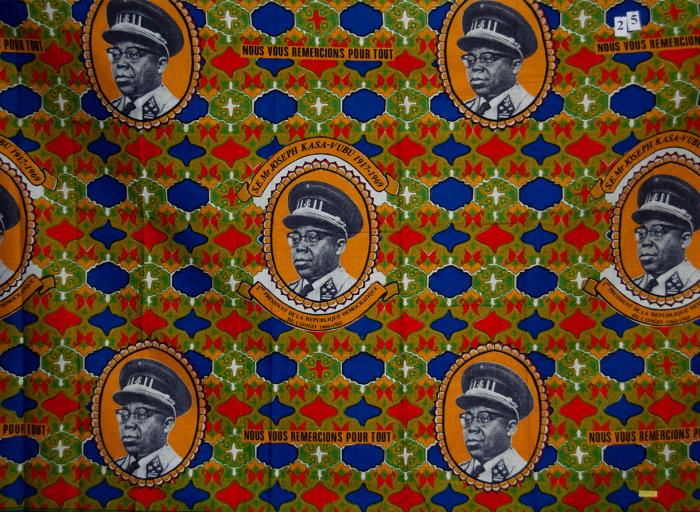
Independence of Congo. Since the end of the war, production had been increased from 12 million meters of woven fabric per year to 32 million meters.
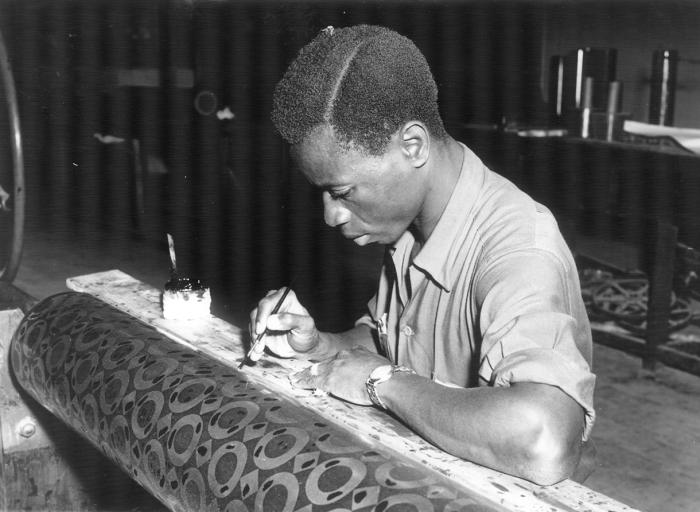
The textile company was initially nationalized, before being returned to TEXAF due to its economic and social importance for the nation.
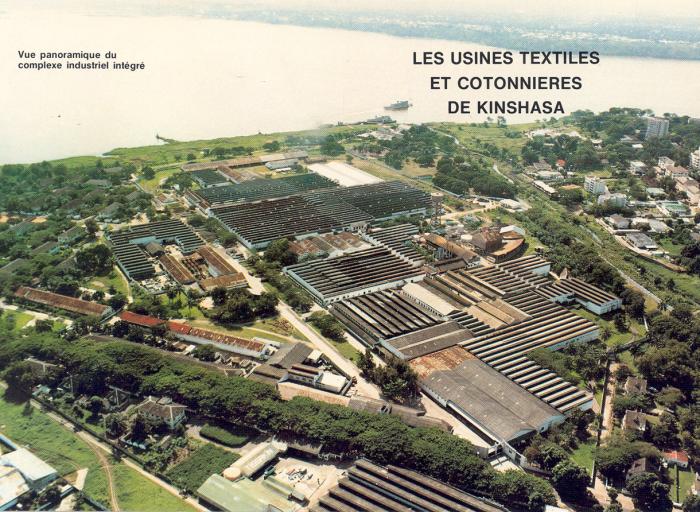
Pillaging in Zaire. The textile factory was protected but two employees were killed and the distribution network was destroyed. The country’s economy collapsed and textile production went into decline.
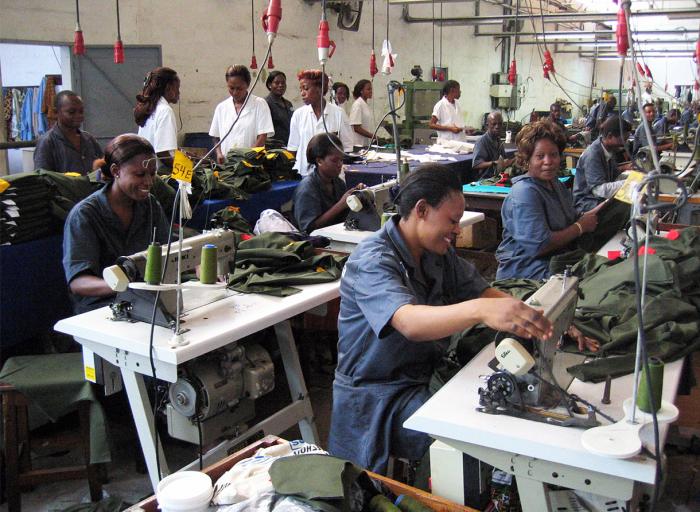
In a management buyout, Philippe Croonenberghs took control of a TEXAF that had been bled dry. It marked the beginning of a new real estate development strategy and a textile alliance with the Hong Kong-based Cha family.
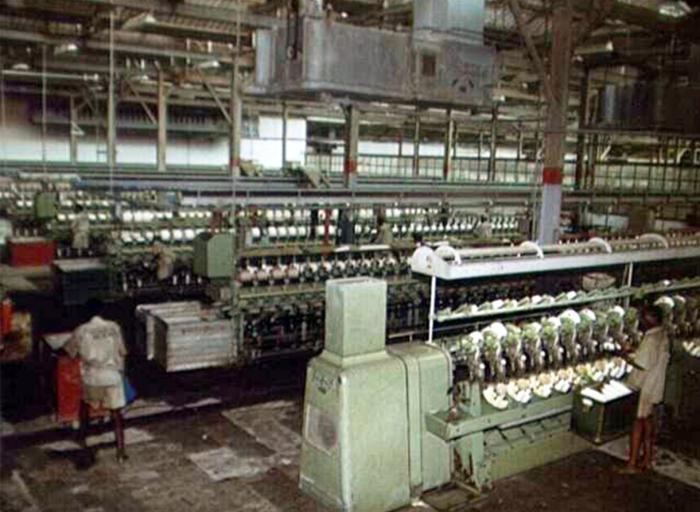
Faced with illegal import dumping and an unfavorable economic environment, the Cha family decided to close the textile factory.
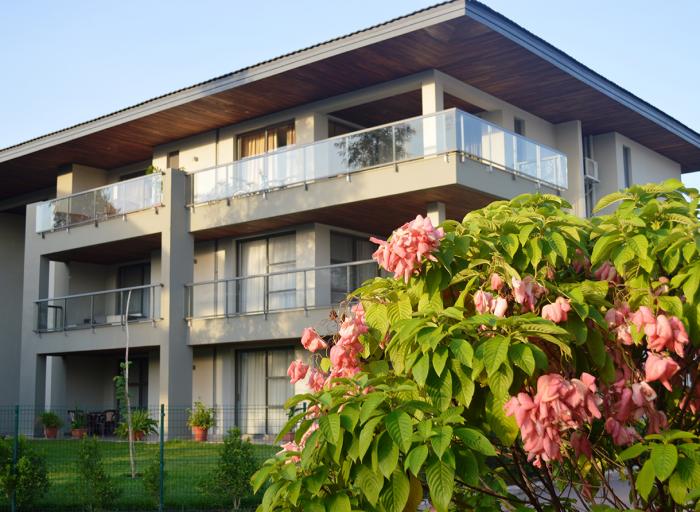
The first new high-end apartment building was leased out in the Musiciens district. The group would follow this with more ambitious construction projects. At the same time, TEXAF increased its 50% stake in Carrigrès to 100%.
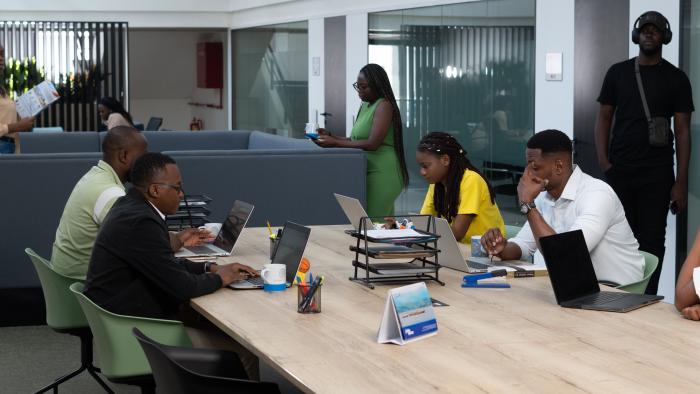
TEXAF decided to invest in the digital economy and to build Central Africa's largest digital campus : the Silikin Village.
TEXAF inaugurated its three largest projects to date : the 94 apartments of the Promenade des Artistes district, the 6,000 sqm of the third phase of Silikin Village and the first international standards data centre of DRC : Open Access Data Centres Texaf Digital.